并联机构可以看作一个闭环运动链机构[1]。影响并联机构精度的因素主要有制造和装配误差及驱动误差[2]。一些学者在分析误差时,通常考虑关节误差和支链误差对末端位姿的影响,忽略关节内部结构参数或导轨方向误差对运动学精度的影响[3-5]。Judd和Knasinski[6]指出在众多误差当中几何参数误差是降低并联机构精度的主要因素。目前提高并联机构精度的主要方法有2种[7]:第1种为直接提高并联结构各零部件的制造及安装精度,但这会大幅度地提高加工成本,对装配人员的能力也具有很大的要求;第2种为对已装配好的并联机构进行参数标定,一般为运动学标定。这种方法成本低、效率高,是人们目前普遍采用的方法。标定分为误差建模、误差测量、参数辨识和误差补偿这4个步骤。
郭江真等[8]基于螺旋理论,以3PRS/UPS为模型,建立了机构的全雅可比矩阵。Rauf等[9]通过测量部分位姿完成了并联机器人的运动学标定。黄田等[10]提出了一种三平动自由度并联机构的误差建模方法,并揭示了几何误差对末端位姿误差的影响规律,对同类装备的设计和制造具有重要意义。Lin等[11]基于Stewart机构,采用误差影响因子法确定了结构参数对执行端位姿误差的影响。宋晓飞等[12]采用激光跟踪仪对6-PSS并联机构进行运动学标定,并用实际算例对所提出方法进行了验证,得到了更准确的杆长误差标定值。Abtanhi等[13]采用测距仪测量并联机构末端位置误差,进行运动学标定,此方法成本低且简单有效。周万勇[14]对6PUS并联机构建立了42参数的误差雅可比矩阵,标定后精度提高了10倍,但其并未考虑导轨安装带来的误差。He等[15]提出基于指数模型(POE)建立串联机器人的误差模型,进行运动学参数辨识的方法。于凌涛等[16]提出三平面测量法辨识机构的误差参数,并在六自由度并联机器人进行了实验验证,结果表明标定后运动精度有明显的改善。刘志杰[17]在位姿误差分析的基础上,提出了基于蚁群算法的并联机器人位姿误差的补偿方法。孙华德等[18]以Stewart并联机构为例提出了2种采用激光跟踪仪测量长度的整机标定方法。刘欢[19]采用机构拆分测量的方式对含有平行四边形支链结构的三平动并联机构进行了标定。
1 误差建模及仿真验证 1.1 6PUS并联机构的结构参数如图 1所示,6PUS并联机构由6根结构完全相同的支链通过下复合虎克铰Bi(i=1,2,…,6)和上复合球铰Ai(i=1,2,…,6)将静平台OC1C2上直线模组CiDi和动平台O′A1A2连接起来。模组导轨方向向量ti(i=1,2,…,6)与静平台平面夹角β=π/6,点C34和A16为C3C4和A1A6的中点,按图 1方式在静、动平台上分别建立固定坐标系Oxyz和连体坐标系O′x′y′z′。ti与Oz轴夹角为θ,t′i与Ox轴夹角为ψ。即导轨的方向向量可表示为

![]() |
图 1 6PUS并联机构示意图 Fig. 1 Schematic of 6PUS parallel mechanism |
对式(1)取微分得
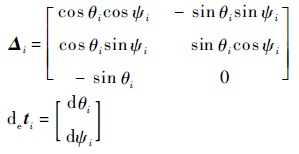
其中:deti为导轨方向误差。
以6个驱动滑块在最低端时为初始位置。任取第i(i=1,2,…,6)个PUS串联支链分析得

式中:Li为杆长;si为支链在Oxyz坐标系下的方向向量;bi为Bi点在Oxyz坐标系下的坐标;λi为驱动;p为O′x′y′z′坐标系到Oxyz坐标系的相对位置;R为O′x′y′z′坐标系到Oxyz坐标系的旋转矩阵;ai为Ai点在O′x′y′z′坐标系下的坐标。
由式(1)~式(3)可知,每根支链上影响动平台位姿的结构参数有:aix,aiy,aiz,bix,biy,biz,θi,ψi,Li。故6PUS并联机构共6×9=54项结构参数。在无误差的情况下,即理论上结构参数如表 1所示。
i | aix/mm | aiy/mm | aiz/mm | bix/mm | biy/mm | biz/mm | θi/rad | ψi/rad | Li/mm |
1 | 95.101 | 34.200 | -53.431 | 243.448 | 275.664 | 104.298 | π/3 | -2π/3 | 340 |
2 | -17.932 | 99.460 | -53.431 | 117.008 | 348.664 | 104.298 | π/3 | -2π/3 | 340 |
3 | -77.168 | 65.260 | -53.431 | -360.456 | 73.000 | 104.298 | π/3 | 0 | 340 |
4 | -77.168 | -65.260 | -53.431 | -360.456 | -73.000 | 104.298 | π/3 | 0 | 340 |
5 | -17.932 | -99.460 | -53.431 | 117.008 | -348.664 | 104.298 | π/3 | 2π/3 | 340 |
6 | 95.101 | -34.200 | -53.431 | 243.448 | -275.664 | 104.298 | π/3 | 2π/3 | 340 |
1.2 参数误差建模
误差模型即建立关于结构参数误差与执行端位姿误差的雅可比矩阵。
对式(3)两端取微分得

两端左点乘siT,由微分关系[17]可知:siTLidsi=0,siTdRai=((Rai)×si)Tdω,ω为O′x′y′z′坐标系到Oxyz坐标系的相对姿态角。
整理式(4)可得

将式(5)整理为矩阵的形式可得

式中:
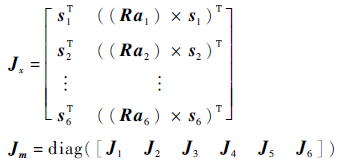
其中:Ji=[-siTsiTR-λisiTΔi],i=1,2,…,6。

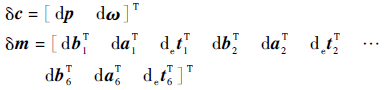
δl为支链杆长误差;δc为动平台的位姿误差;dp=[dx dy dz]为动平台沿xyz坐标轴移动位置误差;dω=[dα dβ dγ]为动平台绕xyz坐标轴的姿态角误差;δm中dbi为静平台虎克铰铰链点误差,dai为动平台球铰铰链点误差。
由于并联机构的可控性要求机构非奇异,即雅可比矩阵Jx可逆,从而式(6)可整理得

式中:J=[Jx-1-Jx-1Jm],J为误差雅可比6×54阶实矩阵。
1.3 算法验证在工作空间中有无穷多个位姿,在仿真和标定实验中,为了减少实验量且保证较大的工作空间,采用正交试验法。每个位姿包含沿坐标轴的移动x、y、z和绕坐标轴的转动α、β、γ六因素。
在参数辨识过程中采用最小二乘法,此方法简单有效,常用于曲线拟合。最小二乘法可表示为:τ=Kθ+n,k为 θ到τ的关系矩阵,n为随机误差。最小二乘法估计可表示为:τ=Kθ,经过m次测量,获得m组测量数据,使各次测量的估计值与测量值之差的平方和最小。即:

式中:
在参数辨识过程中需满足WTW可逆。在仿真中需满足e≤6 m,e为待辨识的结构参数数目。即在仿真和实验中需满足实验位姿数目最小为9。如表 2所示,在仿真中每个因素选为五水平,按正交表可得到25组位姿。
编号 | x/mm | y/mm | z/mm | α/rad | β/rad | γ/rad |
1 | -40 | -20 | 520 | 0.08 | 0.2 | 0.2 |
2 | -20 | -10 | 490 | 0.05 | 0.1 | 0.1 |
3 | 0 | 0 | 460 | 0 | 0 | 0 |
4 | 20 | 10 | 430 | -0.05 | -0.1 | -0.1 |
5 | 40 | 20 | 400 | 0.08 | 0.2 | 0.2 |
如图 2所示,对25组位姿Q1在理论参数E下反解求得驱动。给定参数等于E+δE,δE为给定的结构参数误差值。在给定参数下正解求得动平台位姿,实验中激光跟踪仪测量精度为0.015 mm,引入随机测量误差得到实际位姿Q2,由误差雅可比可知:

式中:δPi为各组实际位姿与理想位姿的差,即δPi=Q2i-Q1i;Ji为各组位姿对应的误差雅可比,由最小二乘法可知:

式中:δE′为辨识的结构参数误差。
此时辨识得到的结构参数为E+δE′,在辨识参数下正解求得迭代位姿Q3,以Q2-Q3<σ作为判据,σ趋近0。通过迭代计算求得结构参数误差∑δE′, 与给定的参数误差δE进行比较。
![]() |
图 2 仿真流程图 Fig. 2 Simulation flowchart |
由于6PUS并联机构的对称性,以支链1的结构参数为例,观察仿真辨识结果,如表 3所示,辨识出的结构参数误差与给定的结构参数误差的最大误差精度在0.000 1,可认为在误差范围内,二者相等。标定模型可准确辨识出结构参数误差,反映出标定模型建立的正确性。
误差对比 | 假设值 | 辨识值 | 差值 |
δaix/mm | 1 | 1.000 | 2×10-4 |
δaix/mm | 1 | 1.000 | 2×10-4 |
δaiy/mm | -1 | -1.000 | 2×10-4 |
δaiz/mm | 1 | 1.000 | 7×10-4 |
δbix/mm | 1 | 1.000 | 2×10-4 |
δbiy/mm | -1 | -1.000 | 2×10-4 |
δbiz/mm | 1 | 1.000 | 2×10-4 |
δθi/rad | 0.01 | 0.010 | 10-6 |
δψi/rad | 0.01 | 0.010 | 2×10-6 |
δLi/mm | 1 | 1.000 | 4×10-4 |
注:辨识值为误差的近似值。 |
2 整机标定实验
不同于传统的拆分标定实验,整机标定依托于误差雅可比矩阵,由控制柜控制驱动使并联机构达到预定位姿,激光跟踪仪测量位姿,直接由位姿误差辨识出结构参数。实验中,激光跟踪仪、控制柜及6PUS并联机构相对位置如图 3所示。
![]() |
图 3 标定位置 Fig. 3 Locations in calibration |
实验开始前,将机构驱动至零位。在实验过程中,为了排除由于激光跟踪仪移动和并联机构移动产生的测量误差,分别设置了3个外界参考点如图 4所示,3个并联机构静平台参考点如图 5所示。
![]() |
图 4 外界参考点 Fig. 4 External reference points |
![]() |
图 5 静平台参考点 Fig. 5 Fix-base reference points |
如图 6所示,静平台有1、2、3、4靶标孔,分别放置靶镜,用激光跟踪仪测量4个位置的坐标。令1为原点O,由1、2连线为Ox轴,1、2、3(4)组成平面法线向上为Oz轴,建立固定坐标系。如图 7所示,动平台上有1、2、3靶标孔,分别放置靶镜,用激光跟踪仪测量3个位置的坐标。以3点拟合的圆心为原点O′,O′x′轴指向1,以O′、1、2(3)组成平面法线向上为O′z′轴,建立连体坐标系。由图 7可以看到,为确定连体坐标系相对于固定坐标系的位姿,动平台上固连4、5、6、7这4个靶标座。
![]() |
图 6 固定坐标系的建立 Fig. 6 Establishment of a fixed coordinate |
![]() |
图 7 连体坐标系的建立 Fig. 7 Establishment of a moving coordinate |
实验采用八水平六因素如表 4所示,按正交表可得到64组位姿。针对每组位姿,在理论参数下驱动滑块达到指定位置,待控制稳定之后,采用激光跟踪仪测量4个固连的靶标座的坐标。在Spatial Analyzer中求解得到实际位姿,从而获得位姿误差。在MATLAB中,根据建立的标定模型辨识结构参数。
编号 | x/mm | y/mm | z/mm | α/rad | β/rad | γ/rad |
1 | -50 | -50 | 495 | 0.15 | 0.20 | 0.20 |
2 | -40 | -40 | 490 | 0.10 | 0.15 | 0.15 |
3 | -20 | -20 | 485 | 0.08 | 0.10 | 0.10 |
4 | -10 | -10 | 480 | 0.05 | 0.05 | 0.05 |
5 | 0 | 0 | 465 | 0 | 0 | 0 |
6 | 20 | 20 | 460 | -0.08 | -0.10 | -0.10 |
7 | 40 | 40 | 450 | -0.10 | -0.15 | -0.15 |
8 | 50 | 50 | 440 | -0.15 | -0.30 | -0.30 |
由于激光跟踪仪的辨识精度在0.015 mm,故无法测量得到精确的实际位姿。进而在辨识过程中Q2-Q3无法收敛到0,此时只需达到收敛即可终止迭代。经MATLAB计算,Q2-Q3收敛到0.08。为证明辨识结构参数的正确性,在MATLAB中,采用辨识结构参数在相同驱动下进行运动学正解求解,计算得到的位姿与测量的实际位姿最大位置误差在0.015 mm左右,刚好为激光跟踪仪的辨识精度。辨识的结构参数如表 5所示。
i | aix/mm | aiy/mm | aiz/mm | bix/mm | biy/mm | biz/mm | θi/rad | ψi/rad | Li/mm |
1 | 94.796 | 34.153 | -53.367 | 239.240 | 269.024 | 108.955 | 1.041 4 | -2.096 4 | 339.816 |
2 | -18.039 | 99.319 | -53.400 | 112.966 | -341.515 | 108.212 | 1.040 5 | -2.097 1 | 340.544 |
3 | -77.044 | 65.261 | -53.435 | -345.858 | -73.462 | 113.912 | 1.048 4 | 0.004 1 | 340.167 |
4 | -77.079 | -65.226 | -53.307 | -341.796 | -72.226 | 116.785 | 1.048 4 | 3.7×10-4 | 340.785 |
5 | -18.007 | -99.142 | -53.263 | 112.938 | -340.372 | 112.367 | 1.050 5 | 2.093 0 | 340.047 |
6 | 95.021 | -34.090 | -53.392 | 239.279 | -268.456 | 111.576 | 1.051 1 | 2.094 7 | 340.337 |
采用五水平六因素的正交试验,按正交表得到25组位姿,对其进行误差补偿,观察标定效果。针对每组位姿,分别在理论参数和辨识参数下驱动滑块,采用激光跟踪仪测量实际位姿。比较2次实际位姿与给定位姿的位置误差和姿态误差。如图 8和图 9所示,标定后,位置精度提高了3个数量级,姿态精度提高了2个数量级。
![]() |
图 8 标定前后的位置误差 Fig. 8 Position errors before and after calibration |
![]() |
图 9 标定前后的姿态误差 Fig. 9 Angle errors before and after calibration |
如表 6所示,选取了标定后位置误差和姿态误差较大的3组典型位姿误差进行比较,可以看到单方向位置精度在0.030 mm,姿态精度在0.000 7rad;三方向位置精度在0.046 mm,姿态精度在0.000 8rad。激光跟踪仪的辨识度为0.015 mm,由数据处理结果可以看到标定效果显著。
序号 | Δx/mm | Δy/mm | Δz/mm | Δα/rad | Δβ/rad | Δγ/rad | ||||||
理论值 | 补偿值 | 理论值 | 补偿值 | 理论值 | 补偿值 | 理论值 | 补偿值 | 理论值 | 补偿值 | 理论值 | 补偿值 | |
5 | 9.431 3 | -0.026 7 | 1.164 0 | 0.030 1 | 18.140 4 | -0.021 7 | -0.038 2 | 0.000 3 | 0.009 9 | 0.000 1 | 0.017 7 | 0.000 7 |
17 | 10.422 1 | 0.009 0 | 1.779 4 | 0.005 1 | 17.618 8 | -0.010 7 | -0.034 4 | 0.000 2 | -0.013 8 | -0.000 6 | 0.016 1 | 0.000 4 |
24 | 13.328 3 | -0.000 1 | 2.645 8 | 0.001 2 | 15.202 9 | -0.018 4 | -0.035 5 | 0 | -0.012 6 | -0.000 4 | 0.014 1 | 0.000 6 |
3 结 论
本文针对6PUS并联机构建立了54结构参数的误差雅可比矩阵,并在MATLAB中进行了仿真实验,最后进行了整机标定研究,得到了如下结论:
1) 在MATLAB中采用最小二乘法进行参数辨识,建立了标定模型,通过仿真证明辨识结果误差在10-6以上,说明了标定模型的正确性。
2) 整机标定实验后,单方向位置精度达到了0.030 mm,姿态精度达到了0.000 7 rad;三方向位置精度达到了0.046 mm,姿态精度达到了0.000 8 rad。通过标定,并联机构的运动学精度得到了明显的提高。
3) 首次提出整机形式标定54结构参数,对比传统的拆分标定实验,整机标定操作简单、标定效果良好。同时,整机标定具有很强的适应性,可针对其他类型的并联机构进行标定,为以后的运动学标定实验提供了一种准确方便的方法。
[1] | MERLET J P. Parallel robots[M]. Berlin: Springer Netherlands, 2006 : 1 . |
Click to display the text | |
[2] | 裴葆青, 陈五一, 王田苗. 6UPS并联机构杆长误差标定及其对动平台运动的影响分析[J]. 组合机床与自动化加工技术,2005 (9) : 45 –51. PEI B Q, CHEN W Y, WANG T M. Calibration of the 6PUS parallel grinding machine by vector method[J]. Modular Machine Tool & Automatic Manufacturing Technique,2005 (9) : 45 –51. (in Chinese). |
Cited By in Cnki (0) | Click to display the text | |
[3] | FAN K C, ZHAO J W, CHANG T H, et al. Error analysis of a serial-parallel type machine tool[J]. The International Journal of Advanced Manufacturing Technology,2002, 19 (3) : 174 –179. |
Click to display the text | |
[4] | RYU J, CHA J. Volumetric error analysis and architecture optimization for accuracy of HexaSlide type parallel manipulators[J]. Mechanism and Machine Theary,2003, 38 (3) : 227 –240. |
Click to display the text | |
[5] | HUANG T, CHETWYND D G, WHITEHOUSE D J, et al. A general and novel approach for parameter identification of 6-DOF parallel kinematic machines[J]. Mechanism and Machine Theory,2005, 40 (2) : 219 –239. |
Click to display the text | |
[6] | JUDD R P, KNASINSKI A B. A technique to calibrate industrial robot with experimental verification.Robotics and automation[J]. IEEE Transactions on Robotics and Automation,1990, 6 (1) : 20 –30. |
Click to display the text | |
[7] | 顾云鹭.六自由度并联地震模拟振动台全误差分析及标定研究[D].上海:上海交通大学,2012:13. GU Y L.Research on the total error analysis and calibration of a parallel 6-DOF earthquake simulator[D].Shanghai:Shanghai Jiao Tong University,2012:13. (in Chinese). |
Cited By in Cnki (0) | Click to display the text | |
[8] | 郭江真, 王丹, 樊锐, 等. 3PRS/UPS冗余驱动并联机器人刚度特性分布[J]. 北京航空航天大学学报,2014, 40 (4) : 500 –506. GUO J Z, WANG D, FAN R, et al. Stiffness characteristics distribution of a 3PRS/UPS parallel manipulator with actuation redundancy[J]. Journal of Beijing University Aeronautics and Astronautics,2014, 40 (4) : 500 –506. (in Chinese). |
Cited By in Cnki (0) | Click to display the text | |
[9] | RAUF A, PERVEZ A, RYU J. Experimental results on kinematic calibration of parallel manipulators using a partial pose measurement device[J]. IEEE Transactions on Robotics,2006, 22 (2) : 379 –384. |
Click to display the text | |
[10] | 黄田, 李亚, 李思维, 等. 一种三自由度并联机构几何误差建模、灵敏度分析及装配工艺设计[J]. 中国科学(E辑),2002, 32 (5) : 628 –636. HUANG T, LI Y, LI S W, et al. Geometric error modeling,sensitivity analysis and assembly process design of a 3-DOF parallel mechanism[J]. Science in China(Series E),2002, 32 (5) : 628 –636. (in Chinese). |
Cited By in Cnki (0) | Click to display the text | |
[11] | LIN H,MENG C,CHUAN H.Error analysis of parallel manipulators based on differential operators[C]//2009 IEEE International Conference on Mechatronics and Automation.Piscataway,NJ:IEEE Press,2009:1302-1306. |
Click to display the text | |
[12] | 宋晓飞, 石万凯, 刘开友. 6-PSS并联机构误差标定方法[J]. 重庆理工大学学报(自然科学版),2012, 26 (6) : 45 –49. SONG X F, SHI W K, LIU K Y. Kinematic calibration of 6-PSS parallel mechanism[J]. Journal of Chongqing Institute of Technology(Natural Science),2012, 26 (6) : 45 –49. (in Chinese). |
Cited By in Cnki (0) | Click to display the text | |
[13] | ABTANHI M, PENDAR H, ALASTY A, et al. Experimental kinematic calibration of parallel manipulators using a relative position error measurement system[J]. Robotics and Computer-Integrated Manfacturing,2010, 26 (6) : 799 –804. |
Click to display the text | |
[14] | 周万勇.并联机构几何精度研究[D].北京:北京航空航天大学,2015:111-118. ZHOU W Y.Research on geometric accuracy of parallel mechanism[D].Beijing:Beihang University,2015:111-118. (in Chinese). |
Cited By in Cnki (0) | Click to display the text | |
[15] | HE R B, ZHAO Y J, YANG S N, et al. Kinematic-parameter identification for serial-robot calibration based on POE formula[J]. IEEE Transactions on Robotics,2010, 26 (3) : 411 –423. |
Click to display the text | |
[16] | 于凌涛, 孙立宁, 杜志江, 等. 并联机器人误差检测与补偿的三平面法[J]. 哈尔滨工程大学学报,2006, 27 (5) : 671 –675. YU L T, SUN L N, DU Z J, et al. Three planes method on measuring and compensation of parallel robot[J]. Journal of Harbin Engineering University,2006, 27 (5) : 671 –675. (in Chinese). |
Cited By in Cnki (0) | Click to display the text | |
[17] | 刘志杰.并联机器人位姿误差分析与补偿方法研究[D].秦皇岛:燕山大学,2010:37-45. LIU Z J.Study on pose error analysis and compensation of parallel robot[D].Qinhuangdao:Yanshan University,2010:37-45. (in Chinese). |
Cited By in Cnki (0) | Click to display the text | |
[18] | 孙华德, 陈五一, 陈鼎昌. 用激光跟踪仪标定并联机床的理论探讨[J]. 机床与液压,2002 (5) : 16 –19. SUN H D, CHEN W Y, CHEN D C. Theoretical investigation about PKM calibration using laser tracker[J]. Machine Tool & Hydraulics,2002 (5) : 16 –19. (in Chinese). |
Cited By in Cnki (0) | Click to display the text | |
[19] | 刘欢.用于三轴机床的广义并联加载机构的设计与研究[D].北京:北京航空航天大学,2014:70-77. LIU H.Design and research of generalized parallel loading mechanism used for three-axis machine tool[D].Beijing:Beihang University,2014:70-77. (in Chinese). |
Cited By in Cnki (0) | Click to display the text | |