针对飞机复合材料构件设计制造过程数据繁多过程复杂的问题,国内外许多人致力于将计算机辅助系统引入到该领域.Kim,富威,Narayana,Setiawan,Milani等人[1,2,3,4,5,6]开发了一系列的计算机辅助系统和优化算法以实现优化设计复合材料构件或者选择最佳材料的目标,而Poudel等人[7]还开发了用于飞机复合材料构件缺陷检测领域的专家系统.而在复合材料构件制造方面,Choi等人[8]开发了用于评价飞机复合材料构件制造成本的知识库系统,还有梅立等人[9]开发了计算机辅助飞机复合材料成型工艺设计系统,以达到选择最佳的成型工艺方法,降低加工成本的目的.但是该系统选择成型工艺方法的推理算法为产生式规则法,在选择成型工艺方法方面存在一定的不足.例如某条规则为:IF纤维含量=高AND树脂黏度=高THEN成型工艺=RTM成型,属性模糊范围划分界限存在一定的歧义.“纤维含量=高”,必定存在某些界限值来界定纤维含量的高中低,假设当纤维含量>90%为“纤维含量=高”,那么纤维含量=89.9%必定界定为“纤维含量=中”.但是从生产实际来看,89.9%与90%相差并不大,某种程度上89.9%也属于“纤维含量=高”的范围,所以一些数值型属性值范围界定太绝对,那么选择结果必然产生误差.另外影响复合材料成型工艺方法选择的因素至少有9个,每种因素都按高中低3层次划分,则共有39=19683种不同的组合结果,再将这些组合结果划分为6种成型方法,工作量较为庞大.故本文认为基于IF-THEN方式的推理方式不适用于复合材料选择成型工艺方法选择.
本文通过研究总结发现飞机复合材料构件成型工艺选择的问题可以利用多属性决策方法解决,而王共冬等人[10]也提出了运用模糊综合评判法选择最佳的成型工艺方法的观点,并且实例验证了其观点的有效性和客观性,但是其建立的复合材料成型方法的综合评价模型完全依靠人为操作,将其转换为计算机可识别的推理算法仍然存在着不足和缺陷,需要改进和完善.
本文在原有的模糊综合评判法的理论基础上,通过借鉴潘正华、张英俊、伍晓榕、荆洪英、杨威等人[11,12,13,14,15]关于模糊推理和多属性决策领域的隶属度计算以及权重分配方面的研究,对评价矩阵的建立和权重分配阶段进行了改进,使其更适用于计算机运算操作.
1 成型方法评价指标的确定
评价指标集是指评估待选方案时所涉及的属性的具体名称,而评估元指标集是指将一系列评估指标集分类分组的名称.评价元指标集是分级的,一级评价元指标集下可包含若干二级评价元指标集,二级评价元指标集下可包含若干三级评价元指标集,最后一级评价元指标集即底层评价元指标集,只包含若干评价指标,而没有下一级评价元指标集.
1.1 一级评价元指标集确定
复合材料成型工艺直接决定了构件的成型质量、生产成本以及生产效率,所以复合材料构件计算机辅助成型工艺设计系统的关键环节即为成型工艺方法的选择.
在实际生产中,影响复合材料成型工艺方法选择的主要因素(即评价指标集)有很多,本文将其划分为两个层次.一级评价元指标集为构件外形特征、构件设计要求、构件生产要求和构件生产成本.
1.2 底层评价元指标集确定
构件外形特征为影响成型工艺的第一要素.主要包含的底层评价元指标集有制件形状、制件尺寸和制件厚度.
设计人员所选用的材料、构件的表面质量以及对构件强度性能的要求也在很大程度上影响了成型方法的选择结果.所以构件设计要求下的底层评价指标集为强度要求、表面粗糙度、使用材料.
在实际生产过程中,产量、生产率要求和计划到投产时间构成了构件生产要求下的底层评价指标集.
扩大复合材料应用范围的重要措施就是降低制造成本,影响复合材料成型工艺生产成本的主要因素有:工人工资、设备成本、模具成本.所以选择生产成本最低的成型工艺必须综合考虑这3种因素.
还有一些因素影响了成型工艺的选择,但影响不大,故本文忽略不计.
综上所述,复合材料成型工艺方法的评价指标体系,共分为两层,一级评价元指标集包含4个方面,底层评价元指标集包含了12种评价指标,如图 1所示.
![]() |
图 1 飞机复合材料成型工艺评价体系Fig. 1 Evaluation system of aircraft composite component |
根据生产实际,工厂最为常用的复合材料成型工艺有6种,分别为:真空袋成型、热压罐成型、拉挤成型、模压成型、纤维缠绕成型、RTM成型.本文将这6种成型工艺作为目标方案.飞机复合材料成型工艺方案的选择过程即为多目标多层次的综合评价过程,整个评价体系结构采用模糊多目标多层次综合评价数学模型.其中涉及主要概念有:因素集、评价集.因素集即为影响评价结果的因素集合,本文中一级因素集为外形特征因素、构件设计要求因素、构件生产要求因素和构件生产成本因素,二级因素集为上一部分的12种评价指标,可按如下方式表达:


评价集即为对于待选成型工艺方案的所有可能的评判结果的集合,总共分为5级:V={vk}={很好,好,较好,差,很差}
模糊评判法在复合材料构件计算机辅助工艺设计系统中的主要计算流程如图 2所示.
![]() |
图 2 模糊综合评价法计算流程Fig. 2 Computing process of fuzzy comprehensive evaluation |
在文献[10]中底层评价矩阵确定过程为:组织多位专家对同一层下的n个指标进行评价,每一个专家会得出一个判断矩阵,然后对各位专家判断矩阵进行统计整理得到最终的评价矩阵.文献中的评价矩阵确定过程完全依靠专家人为评定,对于每一种新的构件都需要重新评定,过程繁长,生产效率低下,并且无法直接应用于计算机运算,故需要对底层评价矩阵确定环节进行改进,将专家经验知识固化表达为计算机算法,通过计算机来实现这一过程.
每种成型工艺的每个因素的评价值都可以划分为很好、好、较好、差、很差5个等级来表征当前构件状态值对某种成型工艺方案的适应度,而根据实际情况,适应度取值范围分布应该如图 2所示,所以每个因素的取值范围应该划分为左很差、左差、左较好、左好、很好、右好、右较好、右差、右很差9个评价范围,但是评价集不变V={vk}={很好,好,较好,差,很差},左很差、右很差∈很差,其他评价范围同样.由于这些评价范围是固定的,故只需要组织专家团队评定出每种因素对应于6种成型工艺的9个评价范围,即完成了专家知识经验的固化.但是这样同样带来了类似于产生式规则法的范围界定太绝对的问题,通过借鉴模糊推理的隶属度函数的方法可以很好地解决这个问题.计算输入因素值隶属于9个评价范围的隶属度,将计算结果按5个评价等级相加即得到了该因素值隶属评价集中各元素的隶属度,如:Vi(y)L-Worst+Ai(y)R-Worst=Ai(y)Worst,其中Ai(y)p-e表示y值属于p-e对应评价范围的隶属度,p的取值为L或R,L表示左,R表示右,e的取值范围为Best,Better,Good,Bad,Worst,分别表示很好、好、较好、差和很差评价范围.为了避免范围界定太绝对的问题,在专家划分范围的基础上,每个评价范围都增加一定的安全裕度以规避模糊界定线,如图 3所示.
![]() |
图 3 评价范围分布示意图Fig. 3 Sketch map for evaluation limits distribution |
规定在评价范围分界线处即x=lp-e时,x隶属于lp-e左边的评价范围的隶属度为1,隶属于lp-e右边评价范围的隶属度为0.8(x>lR-Better时,情况相反).
若某一底层评价指标元uij的状态值为xij,计算其隶属度的函数为分段函数具体如下:
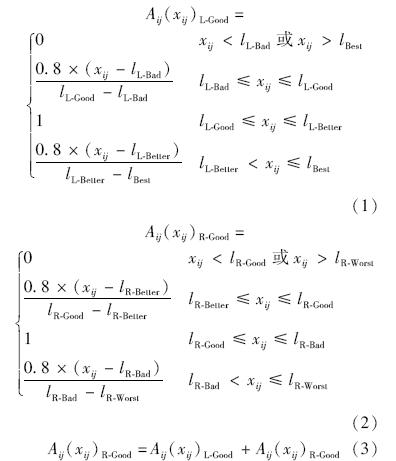
因素值xij隶属于其他评价范围的隶属度计算与上述计算过程相似.
在计算出各个底层评价指标元的状态值隶属于各个评价范围的隶属度后,为了得到底层评价矩阵,需要对各因素值的隶属度进行归一化处理来表征当前状态值对各成型工艺的相对适应程度.归一化处理如下:

由此得每一个一级因素集下的底层评价矩阵:

通过上述处理过程,专家划定评价集的评价范围基本不变,将其存储到计算机中,即实现了专家经验知识的固化,借助隶属度计算规避了指标元评价范围界定太绝对的问题,整个底层评价矩阵的计算过程完全可以应用到计算机系统中,实现了知识重用,有助于生产率的提高.
2.2 权重分配的改进
在模糊评判法中一般是依靠统计或继承的方法计算权重,但是复合材料成型工艺选择过程是一个多目标多层次复杂的评价过程,统计或继承的方法很难得出精确结果.文献[10]中采用了1~9比率标度法进行计算,但是该方法仅仅是依靠专家评定各因素的权重大小无法反映实际设计需要,所以权重的给定应该由系统的使用者即设计者来完成,但是在利用比率标度法的过程中对每个因素进行两两比较并给定相对重要标度,工作量大较为繁琐.为了解决这一问题,本文提出了一种新的权重分配的方法即动态权重分配法.以一级因素集U的各因素的动态权重分配为例进行说明.
步骤1 以每种因素作为度量标准,将比当前因素优先的因素置于该因素右边,不重要的置于左边,同等重要的置于左边(见表 1).这个一对多的对比过程,设计人员很容易实现.
左边 | 度量标准 | 右边 |
U3,U4 | U1 | U2 |
U1,U3,U4 | U2 | |
U3 | U1,U2,U4 | |
U3 | U4 | U1,U2 |
步骤2 统计比较结果.


步骤3 计算机给出最重要因素U2和最不重要因素U3,设计人员根据1~9比率标度法给出U2相对于U3的重要性标度b32(1<b≤9).由此可将[NU3,NU2]=[-3,3]数值范围平均分为b32-1段,每一个节点代表了一个标度.假设b32=5,则可得表 2.
其他b3i按就近原则确定,NUi离哪个数值节点近,b3i即取其对应的标度,中间值取右边的节点.则可得:b31=4,b32=5,b33=4,b34=3.这样其他因素之间的相对重要性也可以通过每个因素相对最不重要因素的标度计算出,计算方法为:bji=1+(b3i-b3j),其中b3i≥b3j.计算结果如表 3所示.
空白处的bji=1/bij,则可得矩阵:
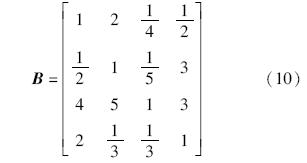
这一步骤只需设计人员给出最重要因素对于最不重要因素的相对重要性标度,然后计算机便可以计算出其他任意两两因素的相对重要性标度,构建出表征权重的矩阵,这个过程实现了用数值大小衡量因素之间的相对重要性,适用于计算机计算.
步骤4 求解矩阵B的特征向量,再进行归一化处理即可得到各因素的权重值.
通过对原有模糊评判法权重分配环节改进,使其能反映实际设计需求并且适应于计算机计算,节省了大量的时间,有效地提高了成型工艺方案选择的效率.
3 系统应用
现利用所开发的系统对一实例进行成型工艺方法选择,系统操作界面如图 4所示.
![]() |
图 4 复合材料构件计算机辅助成型工艺设计系统界面Fig. 4 Computer-aided forming processing design system for composite component |
实例参数如下:工字梁,最大平面尺寸为1500mm,最大厚度为20mm,强度要求800MPa,表面粗糙度要求为3.2,使用材料型号为3233/碳布,产量为1000,要求高生产率,计划到投产时间为30d.本系统备选工艺方案为常用的6种成型工艺:真空袋成型、热压罐成型、拉挤成型、模压成型、纤维缠绕成型、RTM成型.
3.1 计算评价矩阵
根据2.1节中阐述方法进行评价矩阵计算,其中有些特殊因素(属性)计算方法不同,如制件形状、使用材料和生产成本下的3个因素不能用计算隶属度的方法计算评价矩阵.
制件形状为字符型因素不存在数值范围,所以专家无法划分评价范围,但是可以就制件形状特点进行归类划分.本文在美国麻省理工大学(MIT)对复合材料构件按基本形状的分类基础上,根据项目的特点对复合材料构件形状归类划分如图 5所示.
![]() |
图 5 飞机复合材料构件形状分类图Fig. 5 Classificaiton of aircraft composite component shape |
专家评定出底层10种形状对应每种成型工艺的很差、差、较好、好、很好5级评价等级的评价值,将这些对应关系的评价值存入系统中,对于每种制件形状的评价值,计算机只需对其归类划分然后查询出相应的评价值即可.
使用材料同样为字符型因素,虽然该因素也可通过树脂类别进行分类,但是同类树脂工艺性能仍然存在很大不同,所以不能按照类似于制件形状因素的计算方法计算评价值.材料的工艺性能的影响因素为固化温度、成形压力、树脂黏度和固化收缩率,这些因素为数值型,所以可以利用模糊评判法,以固化温度、成形压力、树脂黏度和固化收缩率为因素集,根据当前材料的因素值计算其对应每种成型工艺的评价值(当前使用材料的因素值,可以通过型号在集成系统中的材料库中查询).
生产成本下的3个因素不随制件不同改变,它们只对应不同的成型工艺评价值不同,故将专家直接给出这3种因素对应每种成型工艺的评价值存储在系统中即可.
按照上述计算方法,系统计算出的总体评价矩阵见表 4.
成型工艺 | 总体评价 | 因素 | |||||||||||
S1 | S2 | S3 | D1 | D2 | D3 | P1 | P2 | P3 | C1 | C2 | C3 | ||
真空袋成型 | 很差 | 0 | 0 | 0 | 0.764 | 0 | 0.479 | 0.48 | 0.46 | 0 | 0 | 0 | 0 |
差 | 0.17 | 0 | 0 | 0.210 | 0.012 | 0.094 | 0.37 | 0.37 | 0.16 | 0.16 | 0 | 0 | |
较好 | 0.34 | 0 | 0 | 0.026 | 0.168 | 0.136 | 0.15 | 0.17 | 0.20 | 0.20 | 0.15 | 0.14 | |
好 | 0.28 | 0.708 | 0.109 | 0 | 0.813 | 0.140 | 0 | 0 | 0.26 | 0.28 | 0.37 | 0.34 | |
很好 | 0.21 | 0.292 | 0.891 | 0 | 0.007 | 0.151 | 0 | 0 | 0.38 | 0.36 | 0.48 | 0.52 | |
热压罐成型 | 很差 | 0.070 | 0 | 0 | 0 | 0 | 0.031 | 0.10 | 0.10 | 0.40 | 0.10 | 0.10 | 0.30 |
差 | 0.150 | 0 | 0 | 0 | 0 | 0.081 | 0.15 | 0.15 | 0.35 | 0.15 | 0.15 | 0.5 | |
较好 | 0.180 | 0 | 0.473 | 0 | 0 | 0.103 | 0.20 | 0.20 | 0.20 | 0.20 | 0.20 | 0.15 | |
好 | 0.380 | 0.522 | 0.451 | 0.719 | 0.554 | 0.389 | 0.25 | 0.25 | 0.05 | 0.25 | 0.25 | 0.05 | |
很好 | 0.220 | 0.478 | 0.076 | 0.281 | 0.446 | 0.396 | 0.30 | 0.30 | 0 | 0.30 | 0.30 | 0 | |
拉挤成型 | 很差 | 0 | 0 | 0 | 0 | 0 | 0.022 | 0 | 0 | 0.14 | 0 | 0.10 | 0.07 |
差 | 0 | 0 | 0.118 | 0 | 0.012 | 0.115 | 0.16 | 0.18 | 0.22 | 0.20 | 0.26 | 0.18 | |
较好 | 0.16 | 0 | 0.658 | 0.053 | 0.168 | 0.480 | 0.20 | 0.21 | 0.35 | 0.36 | 0.36 | 0.37 | |
好 | 0.36 | 0.308 | 0.224 | 0.852 | 0.813 | 0.194 | 0.28 | 0.27 | 0.19 | 0.24 | 0.21 | 0.24 | |
很好 | 0.48 | 0.692 | 0 | 0.095 | 0.007 | 0.189 | 0.36 | 0.34 | 0.10 | 0.20 | 0.07 | 0.14 | |
模压成型 | 很差 | 0.07 | 0.105 | 0 | 0.063 | 0 | 0.223 | 0 | 0 | 0.31 | 0 | 0.18 | 0 |
差 | 0.16 | 0.473 | 0 | 0.140 | 0.012 | 0.049 | 0.18 | 0.10 | 0.42 | 0.11 | 0.38 | 0.20 | |
较好 | 0.24 | 0.422 | 0 | 0.605 | 0.168 | 0.101 | 0.26 | 0.25 | 0.27 | 0.28 | 0.24 | 0.35 | |
好 | 0.37 | 0 | 0.273 | 0.192 | 0.813 | 0.362 | 0.32 | 0.27 | 0 | 0.27 | 0.16 | 0.26 | |
很好 | 0.26 | 0 | 0.727 | 0 | 0.007 | 0.265 | 0.24 | 0.38 | 0 | 0.34 | 0.04 | 0.19 | |
纤维缠绕 | 很差 | 0.51 | 0 | 0 | 0 | 0 | 0.054 | 0 | 0 | 0.30 | 0 | 0.15 | 0.11 |
差 | 0.42 | 0 | 0.035 | 0.014 | 0.012 | 0.186 | 0.16 | 0 | 0.38 | 0.20 | 0.36 | 0.17 | |
较好 | 0.07 | 0.049 | 0.335 | 0.176 | 0.168 | 0.192 | 0.20 | 0.20 | 0.24 | 0.36 | 0.27 | 0.34 | |
好 | 0 | 0.788 | 0.630 | 0.810 | 0.813 | 0.348 | 0.28 | 0.34 | 0.08 | 0.24 | 0.14 | 0.24 | |
很好 | 0 | 0.163 | 0 | 0 | 0.007 | 0.220 | 0.36 | 0.46 | 0 | 0.20 | 0.08 | 0.14 | |
RTM成型 | 很差 | 0 | 0 | 0 | 0 | 0 | 0.014 | 0 | 0.10 | 0.43 | 0.25 | 0.44 | 0.04 |
差 | 0.04 | 0 | 0.243 | 0.036 | 0 | 0.100 | 0.09 | 0.22 | 0.36 | 0.37 | 0.38 | 0.17 | |
较好 | 0.36 | 0 | 0.623 | 0.354 | 0 | 0.282 | 0.18 | 0.37 | 0.21 | 0.26 | 0.18 | 0.19 | |
好 | 0.29 | 0.241 | 0.134 | 0.610 | 0.71 | 0.356 | 0.31 | 0.21 | 0 | 0.12 | 0 | 0.36 | |
很好 | 0.31 | 0.759 | 0 | 0 | 0.29 | 0.248 | 0.42 | 0.10 | 0 | 0 | 0 | 0.24 |
按照设计实际要求各因素重要性比较结果如下.
外形特征因素下的3种因素比较结果,如表 5所示.
左边 | 度量标准 | 右边 |
S2,S3 | S1 | |
S3 | S2 | S1 |
S1,S2 | S3 |
设计要求因素下的3种因素比较结果,如表 6所示.
左边 | 度量标准 | 右边 |
D2 | D1 | D3 |
D1,D2 | D3 | |
D1,D3 | D2 |
生产要求因素下的3种因素比较结果,如表 7所示.
左边 | 度量标准 | 右边 |
P2,P3 | P1 | |
P3,P1 | P2 | |
P1,P2 | P3 |
生产成本因素下的各因素权重固定,不需根据设计需求变化,故不需设计人员给定.其下属二级因素集的权重为
WC=[0.11,0.44,0.45]
一级因素外形特征、设计要求、生产要求、生产成本比较结果,如表 8所示.
左边 | 度量标准 | 右边 |
U2,U3,U4 | U1 | |
U1,U4,U3 | U2 | |
U3 | U2,U1,U4 | |
U3 | U4 | U2,U1 |
权重计算结果为:外形特征下各二级因素权重为WS=[0.72,0.14,0.14];设计要求下各二级因素权重为WD=[0.14,0.14,0.72];生产要求下的各二级因素权重为WP=[0.33,0.34,0.33];生产成本下的各二级因素权重为WC=[0.11,0.44,0.45];一级因素集的权重为W=[0.412,0.412,0.065,0.111].
3.3 计算结果
各成型工艺的综合评价结果如表 9所示.
成型工艺 | 很差 | 差 | 较好 | 好 | 很好 |
真空袋成型 | 0.205 | 0.113 | 0.181 | 0.284 | 0.217 |
热压罐成型 | 0.064 | 0.117 | 0.144 | 0.387 | 0.288 |
拉挤成型 | 0.018 | 0.078 | 0.298 | 0.332 | 0.274 |
模压成型 | 0.112 | 0.135 | 0.215 | 0.327 | 0.211 |
纤维缠绕成型 | 0.187 | 0.223 | 0.168 | 0.316 | 0.106 |
RTM成型 | 0.042 | 0.104 | 0.285 | 0.320 | 0.249 |
根据最优原则,制造该构件的成型工艺适应度的次序为:热压罐成型,拉挤成型,RTM成型,真空袋成型,模压成型,纤维缠绕成型.系统推荐选择热压罐成型. 4 结 论
以上系统决策结果完全符合生产实际情况,与工艺人员综合判定的选择结果相同,由此可以得出以下结论:
1) 改进后的模糊综合评判法完全能通过计算机系统实现;
2) 该方法确定的各因素评价范围更符合实际生产情况,克服了原始模糊综合评判法评价范围界定太绝对的缺点;
3) 通过对分配权重环节的改进,计算机可以依据用户偏好快速完成各层次的各因素权重分配,保证了决策效率和决策结果符合用户实际要求.
总体而言,通过将改进后的模糊综合评判法应用到计算机辅助系统,大大提高了复合材料构件成型工艺决策的效率和准确率.
[1] | Kim J S. Development of a user-friendly expert system for composite laminate design[J].Composite Structures,2007,79(1):76-83 |
Click to display the text | |
[2] | 富威,王鹏, 李庆芬.基于Web的复合材料设计专家系统[J].哈尔滨工程大学学报,2004,25(6):773-776 Fu Wei,Wang Peng,Li Qingfen.Study on expert system in composite material design based on the Web[J].Journal of Harbin Engineering University,2004,25(6):773-776(in Chinese) |
Cited By in Cnki (14) | |
[3] | Narayana N G, Omker S N,Mudigere D,et al.Nature inspired optimization techniques for the design optimization of laminated composite structures using failure criteria[J].Expert System with Applications,2011,38(3): 24892499 |
Click to display the text | |
[4] | Setiawan R, Yulianto E.Design of composite brakes using knowledge-based design methodology[J].Advanced Materials Research,2012,566(1):324-330 |
[5] | Milani A S, Eskicioglu C,Robles K,et al.Multiple criteria decision making with life cycle assessment for material selection of composites[J].Express Polymer Letters,2011,5(12): 10621074 |
[6] | Kim J S, Kim C G,Hong C S,et al.Development of concurrent engineering system for design of composite structures[J].Composite Structures,2000,50(3):297-309 |
Click to display the text | |
[7] | Poudel A, Chu T P.Intelligent nondestructive testing expert system for aircraft Carbon/Carbon composite brakes using infrared thermography and air-coupled ultrasound[J].Materials Evaluation,2012,70(10):1219-1229 |
[8] | Choi J W, Kelly D,Raju J,et al.Knowledge-based engineering system to estimate manfacturing cost for composite structures[J].Journal of Aircraft,2005,42(6):1396-1402 |
Click to display the text | |
[9] | 梅立,梅中义, 范玉青.复合材料构件计算机辅助成型工艺设计的研究[J].机械工程师,2009(1):118-121 Mei Li,Mei Zhongyi,Fan Yuqing.Research on computer aided forming process design of composed material structure[J].Mechanical Engineer,2009(1):118-121(in Chinese) |
Cited By in Cnki (3) | |
[10] | 王共冬,刘文剑. 复合材料成型工艺方法的模糊综合评判[J].材料科学与工艺,2008,16(1):66-69 Wang Gongdong,Liu Wenjian.Fuzzy comprehensive evaluation of composite processing on CAPP[J].Materials Science and Technology,2008,16(1):66-69(in Chinese) |
Cited By in Cnki (9) | |
[11] | 潘正华. 模糊推理算法原理[J].计算机研究与发展,2008,45(S1):165-168 Pan Zhenghua.Mathematical principle of the algorithms of fuzzy reasoning[J].Journal of Computer Research and Development,2008,45(S1):165-168(in Chinese) |
Cited By in Cnki (14) | |
[12] | 张英俊,马培军, 苏小红,等.属性权重不确定条件下的区间直觉模糊多属性决策[J].自动化学报,2012,38(2): 220228 Zhang Yingjun,Ma Peijun,Su Xiaohong,et al.Multi-attribute decision making with uncertain attribute weight information in the framework of interval-valued intuitionistic fuzzy set[J]. Acta Automatica Sinica,2012,38(2):220-228(in Chinese) |
Cited By in Cnki (13) | |
[13] | 伍晓榕,张树有, 裘乐淼,等.面向绿色制造的加工工艺参数决策方法及应用[J].机械工程学报,2013,49(7): 91100 Wu Xiaorong,Zhang Shuyou,Qiu Lemiao,et al.Decision making method of process parameter selection for green manufacturing based on a DEMATEL-VIKOR algorithm[J].Journal of Mechanical Engineering,2013,49(7):91-100(in Chinese) |
Cited By in Cnki (1) | |
[14] | 荆洪英,张利, 闻邦椿.基于层次分析法的产品设计质量权重分配[J].东北大学学报:自然科学版,2009,30(5): 712715 Jing Hongying,Zhang Li,Wen Bangchun.AHP-based assignment of weight in product design quality[J].Journal of Northeastern University:Natural Science,2009,30(5):712-715(in Chinese) |
Cited By in Cnki (23) | |
[15] | 杨威,史加荣, 庞永锋.模糊环境下部分权重信息的多属性群决策方法[J].模糊系统与数学,2013,27(1):118-123 Yang Wei,Shi Jiarong,Pang Yongfeng.Fuzzy multi-attribute group decision making with partial weight information[J].Fuzzy Systems and Mathematics,2013,27(1):118-123(in Chinese) |
Cited By in Cnki |