Mathematical model of small diameter condenser pipes
-
摘要: 基于环状流流型建立了小管径冷凝管的数学模型.模型考虑了气液界面表面张力的作用,在同一横截面上气相与液相存在压力差.对两相压降的计算,考虑了气液两相间的相互作用,包括摩擦切应力和动量转移切应力.应用该模型,可考察气相与液相压降、液膜厚度、气相与液相平均速度、气液界面切应力以及管内壁换热系数等的沿程变化情况.根据模拟结果可得:两相压降沿管长呈近似线性增加;气相平均速度沿管长先增大后逐渐减小,但变化范围很小,且远大于液相平均速度;动量转移切应力随液膜厚度增加而增大,同摩擦切应力相比不可忽略;管内壁对流换热系数随液膜厚度增加而减小,由于冷凝管的管径很小,即使蒸气冷凝趋于完毕,气液界面接近冷凝管中心线,换热系数仍较大.Abstract: Based on the annular flow pattern, the mathematical model of condenser pipes with small diameters was established. The effect of surface tension on the liquid/vapor interface causing the pressure difference between liquid and vapor phases on the same cross section and the interaction between the liquid and vapor phases including the frictional and momentum-transfer shear stresses were considered in the model. The variations of the liquid and vapor phase pressure drops, the thickness of the liquid film, shear stress on the liquid/vapor interface and so on along the pipe length can be obtained by solving the model. Based on the modeling results, the conclusions below can be drawn: the two-phase pressure drop along the pipe length increases nearly linearly; the average velocity of vapor phase first increases and then decreases, but the variation range is small and far bigger than that of liquid phase; the momentum-transfer shear stress increases as the thickness of the liquid film increases, and can not be ignored compared to the frictional shear stress; the convective heat transfer coefficient at the inner wall of the pipe decreases as the thickness of the liquid film increases, but it is still comparatively bigger when the condensation is almost completed.
-
Key words:
- condenser /
- simulation /
- pressure drop /
- heat transfer
-
[1] Maydanik Y F. Loop heat pipes [J]. Applied Thermal Engineering, 2005, 25: 635-657 [2] Wang Guanghan, Mishkinis D, Nikanpour D. Capillary heat loop technology: space applications and recent Canadian activities[J]. Applied Thermal Engineering, 2008, 28: 284-303 [3] Pastukhov V G, Maydanik Y F, Vershinin C V, et al. Miniature loop heat pipes for electronics cooling[J]. Applied Thermal Engineering, 2003, 23:1125-1135 [4] Pastukhov V G, Maydanik Y F. Low-noise cooling system for PC on the base of loop heat pipes [J]. Applied Thermal Engineering, 2007, 27: 894-901 [5] Kaya T, Hoang T T, Ku J, et al. Mathematical modeling of loop heat pipes . AIAA-99-0477, 1999 [6] Hoang T T, Kaya T. Mathematical modeling of loop heat pipes with two-phase pressure drop . AIAA-99-33875, 1999 [7] Parker M L. Modeling of loop heat pipe with applications to spacecraft thermal control . Pennsylvania: Faculty of Mechanical Engineering and Applied Mechanics, University of Pennsylvania, 2000 [8] Chuang P A, Cimbala J M, Conroy C T, et al. Comparison of experiments and 1-D steady-state model of a loop heat pipe Proceedings of IMECE. New Orleans, LA:ASME, 2002:1-8 [9] 徐济鋆.沸腾传热和气液两相流[M].2版.北京: 原子能出版社,2001:100-124 Xu Jijun. Boiling heat transfer and liquid/vapor two-phase flow[M]. 2nd ed. Beijing: Nuclear Power Press, 2001:100-124 (in Chinese) -
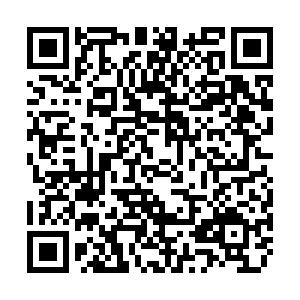
计量
- 文章访问数: 3265
- HTML全文浏览量: 148
- PDF下载量: 1006
- 被引次数: 0