Effects of delamination on compressional properties of composite laminate
-
摘要: 基于影像云纹法、表面应变测量、分级加载超声C扫描3种观测手段,对含有不同位置、尺寸、数量预制分层缺陷的复合材料层板进行了压缩试验研究,对试验中产生的子层屈曲、分层扩展、层板失稳等现象进行了细致的观察、对比与联系.结合试验结果,总结了3种不同的分层扩展模式,并基于分层扩展模式分析了子层屈曲、层板失稳等现象的产生机理.结合上述试验现象,通过比较临界失稳应力、最终破坏应力、分层纵向扩展范围等试验结果,系统地分析了分层缺陷对复合材料层板压缩性能的影响.研究结果可为复合材料结构损伤容限设计提供依据.Abstract: Compressional behaviors of composite laminates were experimentally investigated based on three measuring methods, Shadow Moiré measurement, strain measurement on the surface of laminates and C-scan together with multi-stage loading. Laminates with artificial delamination of various depths, sizes and quantities were studied. The buckling of sub-layer, the extension of delamination and the instability phenomena during the experiments were observed, compared and connected. Three different modes of the extension of delamination were summarized based on the experimental results. The mechanisms of the buckling of sub-layer, the instability of the laminates, etc. were analyzed based on the three modes. The critical buckling stress, the final failure stress and the delamination extension extent through the vertical direction were compared and combined with the experimental phenomenon to analyze the effects of delamination on compressional properties of composite laminate systematically. The results can provide guidance for the damage tolerance designing of composite structures.
-
柔性机构是利用材料的弹性变形传递运动、力或能量的新型机构[1-3]。由于机构中的运动副为一体化的柔性结构故无需装配与润滑,同时避免了摩擦、磨损、间隙、回程误差,减小了机构的体积和重量并可实现高精度运动[4],因此柔性机构在微电子工程[5]、精微操作[6-8]、生物医学工程[9]以及纳米技术[10]等领域得到了广泛的应用。
在微定位领域,特别是对定位精度要求达到微纳米级尺度,且对工作环境要求十分苛刻的超精密定位场合,采用传统的刚性机构需要至少同时考虑由运动副的装配间隙所造成的回程误差,以及由润滑、磨损等造成的高额维护成本和短暂使用寿命等问题,而采用柔性微定位平台则从结构优势上避免了上述问题。空间平动柔性微定位平台由于在精密定位[11]、微纳加工[12]、原子力显微镜的三维扫描[13]等领域的成功应用,其构型设计方法与相关理论分析已成为一大研究热点。郝广波等[14-15]基于自由度与约束空间拓扑法,设计了一种由柔性细长杆组成的3-PPPR型空间平动柔性并联微定位平台,并对平台的伴生转角与耦合误差等进行了分析;Tang等[16]设计了一种3-PPP型空间平动柔性并联微定位平台,由于结构中采用了大行程的柔性移动副,平台在3个移动方向可实现毫米级的运动行程;Awtar等[17]基于约束设计法,提出了一种由柔性薄板组成的空间平动柔性微定位平台,并通过仿真分析了平台的刚度、耦合误差、丢失运动、伴生转角等;Li和Xu[18]设计了一种3-PRC型空间平动柔性并联微定位平台,并通过结构优化、尺寸优化减小了平台的体积与耦合误差,同时对平台进行了运动学、静力学、动力学分析;Gao等[19]根据Delta机器人结构,设计了一种3-PPS型空间平动柔性并联微定位平台,并分析了输入力、负载、刚度和输出位移之间的关系。
综上所述,具有大行程、高固有频率、低运动耦合且结构紧凑优点的新型平台结构设计与分析仍然是空间平动柔性微定位平台的研究重点。为此,本文首先提出一种基于柔性薄板的分布柔度式3-PPP型柔性并联微定位平台;其次通过结构优化减小了平台的体积,并消除了支链中移动副寄生运动的累加;然后基于柔度矩阵法,建立平台的输入刚度模型,同时计算了平台的固有频率,并探究其与柔性薄板尺寸参数之间的关系。最后采用有限元仿真验证结构优化的有效性与理论模型的正确性。
1. 结构设计
目前柔性微定位平台在结构上有串联式[20]、并联式以及串并联混合式[21-22],在类型上有集中柔度式[16]和分布柔度式[17]。相较于串联式与串并联混合式,并联式结构的微定位平台驱动器可固定安装,结构更为紧凑且具有良好的动态性能。相较于集中柔度式,分布柔度式平台具有更少的刚性连杆和更大的运动行程。基于上述本文提出一种由柔性薄板组成的分布柔度式3-PPP型柔性并联微定位平台。
1.1 3-PPP型柔性并联微定位平台的初始结构
3-PPP型柔性并联微定位平台的初始结构如图 1所示,包括基座、动平台和3个柔性支链。每个柔性支链结构相同,均是由柔性薄板组成的平行四边形柔性移动副(P副)串联而成。3个柔性支链正交布置,平台在结构上完全各向同性以保证在3个移动方向上具有相同的静、动态性能。基座的3个正交平面外侧可固定安装压电陶瓷或音圈电机驱动器以分别控制平台在3个方向的移动。
由于平行四边形柔性移动副在变形时会产生轴向的寄生运动,故当平台单轴驱动时,移动副的寄生运动会导致平台在另外2个方向上产生耦合误差。当平台两轴驱动时,以x、y轴方向输入驱动力为例,如图 2所示,支链3中串联的2个被动副在驱动力Fx、Fy作用下均产生沿z轴负方向的寄生运动,分别为ez1和ez2,由于其方向相同,故2个寄生运动相互累加,从而导致平台在z轴方向上出现较大的耦合误差(ez1+ez2)。而当平台三轴同时驱动时,3个支链均会产生被动副寄生运动的累加现象,从而使平台的输入、输出位移不一致,即丢失运动。值得指出的是,这种由寄生运动累加所导致的平台耦合误差与丢失运动增大现象,在现有的多数空间平动柔性微定位平台中普遍存在。
1.2 3-PPP型柔性并联微定位平台的结构优化
为减小平台的耦合误差,提高结构布局的紧凑性,需对平台进行结构优化。基于反向串联方法,通过改变被动副1寄生运动的方向,将两被动副的寄生运动相互抵消(ez1-ez2),如图 3所示。
根据上述原理,结构优化后的柔性支链和微定位平台分别如图 4、图 5所示。优化后的柔性支链中,被动副1采用倒置结构并通过外框与驱动副相连,外框末端设有约束横梁以限制非柔性部件的变形,被动副2与被动副1交叠布置,既实现了两柔性移动副的反向串联,又减小了支链的长度, 使得平台整体结构布局更为紧凑。
2. 刚度分析
刚度属于平台的静态特性,是表征平台在静力作用下运动学特性的关键,并且与机构的自由度、固有频率等密切相关。
目前常用的分析方法有非线性模型法[23]、伪刚体模型法[24-25]和柔度矩阵法[26]。其中非线性模型法具有更高的精度但包含大量的积分项,缺乏直观性[27]。伪刚体模型法将柔性梁单元简化为单自由度的扭簧与刚性连杆的组合[28],无法充分考虑空间受力条件下,梁单元的复合变形。因此本文采用分析过程直观,在小变形条件下又具有较高精度的柔度矩阵法,进行平台的输入刚度分析。
2.1 梁单元的柔度矩阵
如图 6所示,一端固定的等截面悬臂梁,在小变形假设下,其末端中心点受力与变形之间的关系为[26]
(1) 式中:δi为沿i轴的位移;θi为绕i轴的转角;Fi为沿i轴的力;Mi为绕i轴的力矩;6维矩阵为梁单元在O点处的柔度矩阵,其中c1=4l3/(Et3w),c2=4l3/(Etw3),c3=6l2/(Et3w),c4=6l2/(Etw3),c5=l/(Etw),c6=12l/(Etw3),c7=12l/(Et3w),c8=l/(Gk2t3w),E为材料的弹性模量,G为剪切模量,l、t、w分别为梁的长度、厚度、宽度,k2为与梁宽厚比相关的系数。
当w>10t时[29],梁在载荷作用下呈现平面应力状态,应当以平面模量E′代替弹性模量E,二者之间的关系为[30]
(2) 式中:ν为材料的泊松比。
为了得到平台整体的柔度矩阵,需要将结构中所有柔性薄板的柔度矩阵变换到同一点,并根据串、并联关系进行求和,柔度矩阵从坐标系Oi-xyz到Oj-xyz的变换关系为
(3) 式中:COi、COj分别为柔性单元在坐标系Oi-xyz、Oj-xyz原点处的柔度矩阵;POiOj、ROiOj分别为从坐标系Oi-xyz到Oj-xyz的平移、旋转变换矩阵[18]。
2.2 支链的柔度矩阵
如图 7所示,以支链3为例,进行柔度矩阵建模,并将柔性薄板a~h之外的部分视为刚性结构。图中:H为支链的总长,s为外框宽度,u1、u2分别为柔性薄板c和d、e和f的间距。柔性薄板i在坐标系Oi-xyz原点处的柔度矩阵为
(4) 式中:Ci为柔性薄板i在其末端中心点处的柔度矩阵;PiOi为从柔性薄板末端中心点到坐标系Oi-xyz坐标原点Oi的平移变换矩阵。
由于在坐标系O1-xyz下柔性薄板a、b和c、d关于坐标轴O1z对称,a、c关于坐标轴O1x对称,故在O1点柔性薄板a~d的柔度矩阵为
(5) (6) (7) (8) 式中:Ri为绕坐标轴i(i=x、y、z)的旋转变换矩阵。因为柔性薄板a~d并联构成支链3的驱动副,所以驱动副在O1的柔度矩阵为
(9) 由于在坐标系O2-xyz下柔性薄板e、f关于坐标轴O2z对称,故在O2点柔性薄板e、f的柔度矩阵分别为
(10) (11) 因为柔性薄板e、f并联构成支链3的被动副1,所以被动副1在O2的柔度矩阵为
(12) 由于在坐标系O3-xyz下柔性薄板g、h关于坐标轴O3z对称,故在O3点柔性薄板g、h的柔度矩阵为
(13) (14) 因为柔性薄板g、h并联构成支链3的被动副2,所以被动副2在O3点的柔度矩阵为
(15) 为了得到支链的柔度矩阵, 需要将支链中所有运动副的柔度矩阵变换到相同坐标系下的同一点。在坐标系O-xyz原点O处,3个运动副的柔度矩阵分别为
(16) (17) (18) 因为在坐标系O-xyz下3个运动副为串联关系,所以支链3在O点的柔度矩阵为
(19) 由于平台的3个支链结构完全相同,所以支链1、支链2在O点的柔度矩阵分别为
(20) (21) 2.3 平台输入点的柔度矩阵
如图 5所示,为了得到平台在输入点的柔度矩阵,需要将所有柔性单元的柔度矩阵变换到输入点Oz,并根据串、并联关系进行求和。支链1、支链2在O点为并联关系,将两支链并联后视为一个整体,其柔度矩阵为
(22) 支链1、支链2所组成的整体、支链3的驱动副、被动副1、被动副2在平台z轴方向输入点Oz处的柔度矩阵为
(23) (24) (25) (26) 因为支链1、支链2所组成的整体、支链3的被动副1、被动副2关于点Oz为串联关系,且与支链3的驱动副之间为并联关系,所以平台在输入点的柔度矩阵为
(27) 由于平台结构具有各向同性,因此平台在3个平移方向的输入刚度均为
(28) 则平台在输入点处的力-位移关系为
(29) 式中:F为驱动力;δ为输入点的位移。
2.4 输入刚度的有限元仿真验证
为验证微定位平台输入刚度理论模型的正确性,采用ABAQUS对平台进行有限元仿真,选择强度与弹性模量之比较高的AL-7075作为微定位平台的材料。其弹性模量E=71.7 GPa,泊松比ν=0.33,屈服强度为503 MPa,密度为2 810 kg/m3。平台的具体尺寸参数如图 7和表 1所示。将表 1中的数据代入式(5)~式(28),计算得到平台的输入刚度为141.37 N/mm。
表 1 平台的尺寸参数Table 1. Dimension parameters of stage参数 数值/mm t 0.5 w 25 l 40 H 59 u1 45.5 u2 28.5 s 44 平台采用四面体单元进行网格划分,柔性薄板处设置较小的网格划分参数(取1 mm),其余部分网格尺寸为4 mm,以提高结果准确性和分析速度。在驱动副末端与基座接触的面上,施加固定约束,并在外框的底面施加沿z轴方向0~50 N的驱动力。平台的仿真结果如图 8所示。
将位于外框底面中心处的输入点设为仿真参考点,在不同驱动力下,参考点沿z轴方向的位移仿真值、理论计算值及二者的相对误差如表 2、表 3所示。
表 2 参考点位移的矩阵法计算值、仿真值及相对误差Table 2. Matrix method calculation values, simulation values and relative error of reference point displacement驱动力/N 参考点位移/μm 相对误差/% 理论计算值 仿真值 10 70.74 73.15 3.41 20 141.47 143.36 1.33 30 212.21 208.78 1.62 40 282.94 268.73 5.02 50 353.68 323.36 8.57 表 3 参考点位移非线性法计算值、仿真值及相对误差Table 3. Nonlinear method calculation values, simulation values and relative error of reference point displacement驱动力/N 参考点位移/μm 相对误差/% 理论计算值 仿真值 10 70.1 73.15 4.35 20 136.9 143.36 4.72 30 198.3 208.78 5.28 40 253.8 268.73 5.88 50 303.7 323.36 6.47 为更直观地表达参考点位移理论计算值和仿真值之间的关系,根据表 2、表 3中的数据绘制曲线,如图 9所示。
由图 9和表 2、表 3的仿真结果可知,随着行程的增加,平台的刚度呈现较为明显的非线性现象,主要原因是,具有对称结构的驱动副出现了应力刚化效应[30]。在参考点位移仿真值0~268 μm范围内,矩阵法的计算值和仿真值之间最大误差约为5%。因此基于矩阵法的平台刚度分析在小位移时具有较高的精度,而在大行程时则需考虑应力刚化效应进行非线性分析,由于大行程下平台的特性研究不是本文的重点,因此非线性分析的具体过程可参阅文献[31],不再详述。
3. 模态分析
模态是结构的固有振动特性,属于平台的动态特性。对平台进行模态分析,不仅可以避免平台在高频驱动时出现共振现象,而且可以探究结构参数与平台固有频率之间的关系,以指导平台的优化设计。为更加直观地描述平台的结构参数与固有频率之间的关系,平台的前3阶固有频率可简化为[14]
(30) 式中:M为刚性部件在各轴方向的等效质量,由图 4、图 8可知:
(31) 其中:mi为刚性部件i(i=1~6)的质量。
联立式(28)、式(30)和式(31),并结合平台的材料属性与具体尺寸参数计算得到平台的前3阶固有频率为97.92 Hz。
平台有限元仿真的1~6阶模态振型及固有频率分别如图 10、表 4所示。
表 4 平台有限元分析的固有频率Table 4. Natural frequency of stage obtained by finite element analysis阶数 1阶 2阶 3阶 4阶 5阶 6阶 频率/Hz 94.49 94.49 94.49 694.13 700 700.13 由图 10、表 4可知,平台在3个移动自由度方向的固有频率相同,并且与非自由度方向的固有频率有明显的差别,说明平台具有良好的动态特性。平台前3阶固有频率仿真值为94.49 Hz,理论计算值为97.92 Hz,二者相对误差为3.50%,验证了平台模态分析的正确性。
基于上述输入刚度与模态分析理论模型,可以得到平台的固有频率与柔性薄板尺寸参数之间的关系,如图 11所示。
由图 11可知,增加柔性薄板厚度和宽度,减少柔性薄板的长度均可提升平台的固有频率,其中柔性薄板的厚度对平台固有频率影响最为显著。通过探究结构参数对平台固有频率的影响,为平台进行尺寸优化提供了重要依据。
4. 仿真对比
运动耦合是柔性机构的固有属性[15],为了补偿平台的耦合误差往往需要设计复杂的闭环控制系统,因此通过结构优化降低平台的耦合误差有助于简化平台的控制系统设计。
如图 12所示,为分析平台在不同输入条件下的输出特性,对平台分别施加单轴、两轴和三轴的驱动位移,并选取动平台中心为参考点,得到不同输入条件下参考点的耦合位移与丢失运动。并进一步验证结构优化的有效性,对初始结构平台施加相同的驱动位移,同时使两平台在材料选择、柔性薄板的尺寸参数和网格尺寸上均保持相同。
如图 12(a)所示,对平台施加沿x轴方向0~268 μm的驱动位移,参考点的耦合位移与丢失运动仿真结果如图 13、表 5所示。
表 5 单轴驱动时参考点的耦合位移与丢失运动Table 5. Coupling displacement and lost motion of reference point with single-axis actuationμm 平台结构 y轴方向的最大耦合位移 z轴方向的最大耦合位移 x轴方向的最大丢失运动 初始结构 -1.08 -1.09 0.45 优化后的结构 -1.04 0.85 0.23 由图 13、表 5可知,单轴驱动时,相较于初始结构,结构优化后平台的耦合误差有小幅降低,同时,丢失运动较低较为明显,这主要是因为优化后的平台结构更为紧凑,减小了平台的伴生转动,从而使平台具有更优的输入输出一致性。当驱动位移为268 μm时,优化后的平台在y、z轴方向的耦合位移以及x轴方向的丢失运动达到最大分别为-1.04、0.85、0.23 μm,仅占驱动位移的0.39%、0.32%、0.086%。
如图 12(b)所示,沿x轴方向的驱动位移加载完毕后,再施加沿y轴方向0~268 μm的驱动位移,参考点在z轴方向的耦合位移,如图 14所示。
由图 14可知,随着沿y轴方向驱动位移的增加,初始结构平台在z轴方向的耦合位移逐步累加至-2.15 μm,而优化后的平台在z轴方向的耦合位移则逐步减小至接近于0,这表明优化后的平台消除了由柔性移动副的寄生运动累加所导致的平台耦合误差增大现象。
为了进一步探究三轴同时驱动时,驱动位移与平台丢失运动之间的关系(见图 12(c)),在3个方向上对平台同时施加0~268 μm的驱动位移,由于平台具有各向同性,在3个方向上参考点的丢失运动几乎相同,因此将参考点在3个方向的丢失运动取平均值,并得到驱动位移与丢失运动之间的关系,如图 15所示。
由图 15可知,随驱动位移的增加平台初始结构的丢失运动非线性的增大并达到2.54 μm,优化后的平台最大丢失运动仅为0.24 μm。
综合上述对比分析可知:
1) 优化后的平台在单轴和多轴驱动时均具有更优的运动解耦特性和输入输出一致性。
2) 结构优化后的平台总体尺寸为146×146×146 mm3,相较于初始结构尺寸210.5×210.5×210.5 mm3,体积减小了67%,从而验证了平台结构优化的有效性。
5. 结论
1) 设计了一种分布柔度式3-PPP型柔性并联微定位平台,并通过结构优化减小了平台的总体尺寸,同时提高了平台的运动解耦性和输入输出一致性。
2) 基于柔度矩阵法建立了平台小位移下的输入刚度理论模型,同时计算了平台的固有频率,探究了固有频率与平台结构参数之间的关系,为平台的尺寸优化提供了依据。
3) 通过有限元仿真对平台的输入刚度、固有频率、耦合误差与丢失运动进行了分析,验证了理论模型的正确性和结构优化的有效性。
后续将搭建实验平台,对理论模型及平台的相关性能做进一步的测试与验证。
-
[1] 林智育, 许希武.复合材料层板低速冲击后剩余压缩强度[J].复合材料学报,2008,25(1):140-146. Lin Z Y,Xu X W.Residual compressive strength of composite laminates after low-velocity impact[J].Materiae Compositae Sinica,2008,25(1):140-146(in Chinese). [2] 林智育, 许希武,朱伟垚.复合材料层板冲击损伤特性及冲击后压缩研究[J].航空材料学报,2011,31(1):73-80. Lin Z Y,Xu X W,Zhu W Y.Experimental study on impact damage characteristics and residual compressive strength of composite laminates[J].Journal of Areonautical Materials,2011,31(1):73-80(in Chinese). [3] Whitcomb J D. Three-dimensional analysis of a post buckled embeded delamination[J].Journal of Composite Materials,1989,23(9): 862-889. [4] Whitcomb J D. Analysis of a laminate with a post-buckled embeded delamination including contact effects[J].Journal of Composite Materials,1992,26(10): 1523-1535. [5] 孙念先, 陈浩然,陈绍杰.含分层损伤复合材料层合板前后屈曲行为研究[J].航空学报,1999,20(3):224-229. Sun N X,Chen H R,Chen S J.Pre-postbuckling analysis of composite laminates with delamination damage[J].Acta Aeronautica et Astronautica Sinica,1999,20(3):224-229(in Chinese). [6] 孙念先, 陈浩然,苏长健.含分层损伤复合材料层合板剩余压缩强度研究[J].应用力学学报,2000,17(4):138-143. Sun N X,Chen H R,Su C J.Study of residual compression strength of composite laminate strength with delamination[J].Chinese Journal of Applied Mechnics,2000,17(4):138-143(in Chinese). [7] 孙念先, 陈浩然,苏长健.含分层损伤复合材料层合板分层扩展研究[J].力学学报,2000,32(2):223-232. Sun N X,Chen H R,Su C J.Delamination growth in composite laminates[J].Acta Mechanica Sinica,2000,32(2):223-232(in Chinese). [8] 郭兆璞,陈浩然. 含分层损伤复合材料层合板的屈曲特性研究[J].玻璃钢/复合材料,1999(2):3-5. Guo Z P,Chen H R.Buckling behavior of delaminated composite panels[J].Fiber Reinforced Plastics/Composites,1999(2):3-5(in Chinese). [9] 郭兆璞, 陈浩然.含分层损伤复合材料层合板的压缩强度研究[J].固体力学学报,2000,21(2):117-122. Guo Z P,Chen H R.Compressive strength behavior of composite laminates with delamination damage[J].Acta Mechanica Solida Sinica,2000,21(2):117-122(in Chinese). [10] 叶金蕊,李嘉, 刘卫平,等.分层缺损对复合材料结构压缩强度的影响[J].科技导报,2013,31(7):23-27. Ye J R,Li J,Liu W P,et al.Influence of delamination flaw on compressive strength of composite structure[J].Science & Technology Review,2013,31(7):23-27(in Chinese). [11] Asp L E, Nilsson S,Singh S.An experimental investigation of the influence of delamination growth on the residual strength of impacted laminates[J].Composites:Part A,2001,32(9):1229-1235. [12] Abrate S. Impact on laminated composite materials[J].Applied Mechanics Reviews,1991,44(4):155-160. [13] Abrate S. Impact on laminated composites:recent advances[J].Applied Mechanics Reviews,1994,47(11):517-524. [14] 许洪明, 温卫东,刘芳.含分层缺陷复合材料层合板压缩强度试验研究[J].航空发动机,2013,39(3):73-76. Xu H M,Wen W D,Liu F.Compressive strength experimentation research on composite laminates layered defect[J].Aeroengine,2013,39(3):73-76(in Chinese). [15] Benzeggagh M L, Kenane M.Measurement of mixed-mode delamination fracture toughness of unidirectional glass/epoxy composites with mixed-mode bending apparatus[J].Composites Science and Technology,1996,56(4):439-449. -
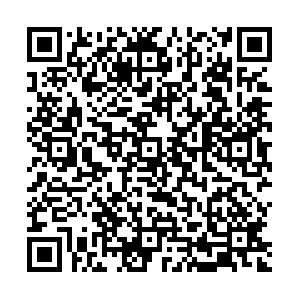
计量
- 文章访问数: 1239
- HTML全文浏览量: 81
- PDF下载量: 584
- 被引次数: 0