Hot diaphragm forming of carbon fiber composite with C-shaped structure
-
摘要: 采用自行设计的热隔膜成型工艺实验装置,制备了C形结构碳纤维复合材料预成型体,测试了成型过程中预成型体和模具温度的变化规律,并考察了成型温度、预成型体尺寸对C形预成型体表面质量和内部缺陷的影响.结果表明:热隔膜成型过程中,采用模具预热的方法与红外灯辐射相配合,可保证预浸料温度的分布均匀性;成型温度过低时,预浸料粘性大、层间滑移能力差,导致预成型体拐角处出现纤维褶皱,并且内部孔隙偏多;预成型体的外形尺寸与模具尺寸接近,则预成型体易受隔膜架桥、变形量过大影响而出现翘曲等缺陷,因此预成型体与模具之间的尺寸比例应控制在一定范围内.Abstract: The device of hot diaphragm forming was designed. The preforms of carbon fiber composite with C-shape structure were fabricated. The variations of temperatures on the preforms and the mould were measured. Furthermore, the influences of the forming temperature and the size of perform on the processing quality and internal defect were investigated. It shows the combination of preheating of mould with the radiation heating effect during the hot diaphragm forming could guarantee the temperature of the prepreg distributes homogeneously. When the forming temperature is low, the viscidity of the prepreg is relatively great and the ability of slipping between prepreg is poor which cause the fiber wrinkle at the corner of preform and high poriness. In addition, the preform tends to warp, when the size of preform is close to that of the mould. This phenomenon results from the diaphragm bridging and large deformation of the preform, hence proper size proportion between preform and mould must be controlled.
-
Key words:
- carbon fiber composite /
- hot diaphragm forming /
- C-shape structure /
- prepreg /
- preform
-
[1] 杜善义,关志东. 我国大型客机先进复合材料技术应对策略思考[J]. 复合材料学报,2008,25(1):1-10 Du Shanyi,Guan Zhidong. Strategic considerations for development of advanced composite technology for large commercial aircraft in China[J]. Acta Materiae Compositae Sinica,2008,25 (1):1-10(in Chinese) [2] 匡载平,戴棣,王雪明. 热隔膜成型技术[C]//杜善义,肖加余. 复合材料:创新与可持续发展(上册). 北京:中国科学技术出版社,2010:613-615 Kuang Zaiping,Dai Di,Wang Xueming. Technology of hot-diaphragm forming[C]//Composite Materials:Innovation and Sustainable Development (Volume 1). Beijing: Popular Science Press,2010:613-615(in Chinese) [3] 吴志恩. 复合材料热隔膜成型[J]. 航空制造技术,2009(增刊2):113-116 Wu Zhien. Hot drape forming of composites[J]. Aeronautical Manufacturing Technology,2009 (Supplement2):113 -116 (in Chinese) [4] 陈亚莉. 复合材料成型工艺在A400M 军用运输机上的应用[J]. 航空制造技术,2008(10):32-35 Chen Yali. Application of composite forming technique in military freighter A400M[J]. Aeronautical Manufacturing Technology, 2008(10):32-35(in Chinese) [5] Krebs J,Friedrich K,Bhattacharyya D. A direct comparison of matched-die versus diaphragm forming[J]. Composites Part A: Applied Science and Manufacturing,1998,29(1/2):183-188 [6] Mallon P J,O'bradaidhand C M,Pipes R B. Polymeric diaphragm forming of complex-curvature thermoplastic composite parts[J]. Composites,1989,20(1):48-56 [7] Pantelakis S G,Baxevani E A. Optimization of the diaphragm forming process with regard to product quality and cost[J]. Composites Part A: Applied Science and Manufacturing,2002,33 (4):459-470 [8] Gutowski T G,Dillon G,Chey S,et al. Laminate wrinkling scaling laws for ideal composites[J]. Composites Manufacturing, 1995,6(2/3):123-134 [9] Bersee H E N,Beukers A. Diaphragm forming of continuous fibre reinforced thermoplastics:influence of temperature, pressure and forming velocity on the forming of Upilex-Rw diaphragms[J]. Composites Part A:Applied Science and Manufacturing,2002,33 (7):949-958 [10] Labeas G N,Watiti V B,Katsiropoulos C V. Thermomechanical simulation of infrared heating diaphragm forming process for thermoplastic parts[J]. Journal of Thermoplastic Composite Materials,2008,21(4):353-370 -
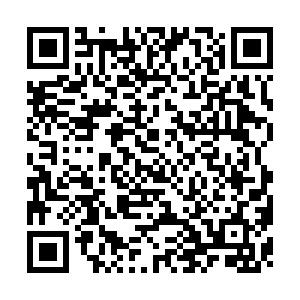
计量
- 文章访问数: 2528
- HTML全文浏览量: 149
- PDF下载量: 1180
- 被引次数: 0