Numerical Simulation of 3D Viscous Flow in Exhaust Casing of a Low-Pressure Steam Turbine
-
摘要: 运用三维粘性流场数值模拟软件(Fine/Turbo)对一个低压蒸汽透平排气缸内的复杂流动进行数值模拟,计算结果与已有的实验数据进行了对比.计算得到的排气缸出口截面上的质量平均总压损失为47.8%,实验值为40.9%.数值模拟清晰地显示了排气缸通道内的流场结构是以各种旋涡为主要特征,包括通道涡、分离涡和端壁涡等.其中,通道涡的尺度最大,是造成排汽缸内能量损失的最主要因素.Abstract: Numerical results of a 3D viscous flow in an exhaust casing of a low-pressure steam turbine were obtained with the 3D Navier-Stokes solver Fine/Turbo. Good agreements with the available experimental data in velocity, static and total pressure coefficients were exhibited. The computational results revealed a complex vortex system within the casing model, including a passage vortex, a separation vortex and an endwall vortex. Of all the vortices, most portion of energy losses within the casing is contributed by the passage vortex. The calculated overall mass averaged total pressure loss in the casing is nearly 47.8%, very close to the experimental value of 40.9%.
-
Key words:
- steam turbines /
- exhaust casing /
- numerical simulation /
- total pressure losses
-
[1] Tindell R H, Alston T M, Sarro C A, et al. Computational fluid synamics analysis of a steam power plant low pressure turbine downward exhaust hood. In:PWR-Vol.13, Design, Repair and Rrefurnishment of Steam Turbines. ASME, 1991.43~55. [2]Xu X, Kang S, Hirsch C. Numerical simulation of the 3D viscous flow in the exhaust casing of a lowpressure steam turbine. ASME 2001-GT-0487, 2001. [3]Liu J, Cui Y, Jiang H. Investigation of flow in a steam turbine exhaust hood with/without turbine exit conditions simulated. ASME 2001-GT-0488, 2001. -
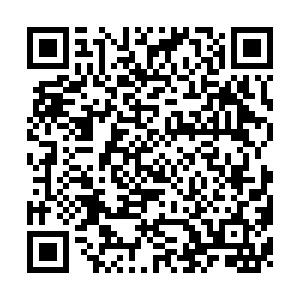
计量
- 文章访问数: 2992
- HTML全文浏览量: 185
- PDF下载量: 974
- 被引次数: 0